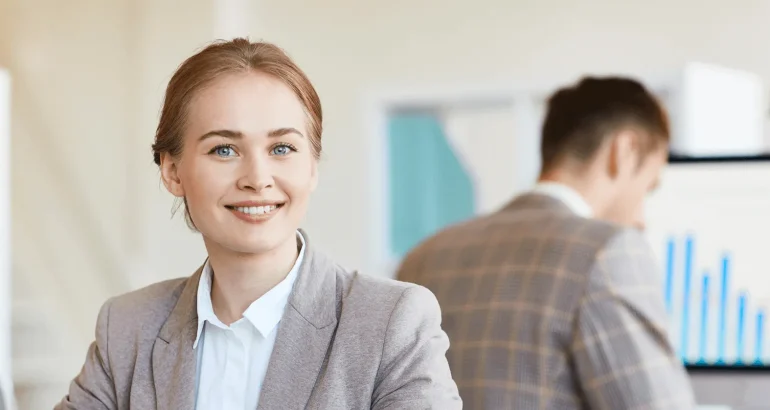
Introduction to Plastic Molds
Plastic molds, also known as plastic injection molds, are essential tools in the manufacturing industry, particularly in the production of plastic components and products. These molds are used to shape molten plastic into specific forms, enabling the mass production of items ranging from simple household goods to complex automotive parts. The process of plastic molding involves injecting molten plastic material into a mold cavity, where it cools and solidifies into the desired shape. This article provides an in-depth overview of plastic molds, including their types, design considerations, manufacturing processes, and applications.
Types of Plastic Molds
Plastic molds can be categorized into several types based on their design, functionality, and the specific molding process they are used for. The most common types include:
- Injection Molds: These are the most widely used molds in the plastic industry. Injection molds are designed to produce high volumes of plastic parts with consistent quality. The process involves injecting molten plastic into a mold cavity under high pressure. Once the plastic cools and solidifies, the mold opens, and the part is ejected. Injection molds are used for a wide range of products, including toys, containers, and automotive components.
- Blow Molds: Blow molding is used to create hollow plastic parts, such as bottles and containers. The process involves inflating a heated plastic tube (parison) inside a mold cavity until it takes the shape of the mold. Blow molds are typically made from aluminum or steel and are designed to withstand the pressures involved in the blowing process.
- Compression Molds: Compression molding is used for thermosetting plastics, which cannot be melted and reshaped once cured. In this process, a pre-measured amount of plastic material is placed in a heated mold cavity. The mold is then closed, and pressure is applied to force the material to fill the cavity. Compression molds are commonly used for producing large, flat parts, such as automotive panels and electrical insulators.
- Rotational Molds: Rotational molding, also known as rotomolding, is used to produce large, hollow plastic parts, such as tanks, containers, and playground equipment. The process involves rotating a mold around two perpendicular axes while heating it. The plastic material inside the mold melts and coats the interior surfaces, forming a hollow part as it cools. Rotational molds are typically made from aluminum or steel and are designed to withstand the rotational forces and temperatures involved in the process.
- Thermoforming Molds: Thermoforming is a process where a plastic sheet is heated until it becomes pliable and then formed into a specific shape using a mold. The mold can be either male (positive) or female (negative), depending on the desired shape of the final product. Thermoforming molds are commonly used for producing packaging materials, disposable cups, and trays.
Design Considerations for Plastic Molds
The design of a plastic mold is a critical factor that determines the quality, functionality, and cost-effectiveness of the final product. Several key considerations must be taken into account during the mold design process:
- Part Design: The design of the plastic part itself plays a significant role in determining the mold design. Factors such as wall thickness, draft angles, undercuts, and surface finish must be carefully considered to ensure that the part can be easily ejected from the mold and that it meets the required specifications.
- Material Selection: The choice of mold material is crucial for ensuring the durability and performance of the mold. Common materials used for plastic molds include tool steel, stainless steel, and aluminum. The selection of material depends on factors such as the type of plastic being molded, the expected production volume, and the required mold life.
- Mold Cooling: Efficient cooling is essential for maintaining consistent part quality and reducing cycle times. Cooling channels are typically incorporated into the mold design to facilitate the rapid and uniform cooling of the plastic material. The placement and design of these channels must be carefully planned to avoid warping or other defects in the final product.
- Ejection System: The ejection system is responsible for removing the finished part from the mold once it has cooled and solidified. The design of the ejection system must ensure that the part is ejected smoothly and without damage. Common ejection methods include ejector pins, sleeves, and air blasts.
- Venting: Proper venting is necessary to allow air and gases to escape from the mold cavity during the injection process. Inadequate venting can lead to defects such as air traps, burns, and incomplete filling of the mold. Venting channels are typically incorporated into the mold design to address this issue.
- Mold Maintenance: Regular maintenance is essential for prolonging the life of a plastic mold and ensuring consistent part quality. Maintenance activities may include cleaning, lubrication, and the replacement of worn or damaged components. The mold design should facilitate easy access to critical components for maintenance purposes.
Manufacturing Processes for Plastic Molds
The manufacturing of plastic molds involves several steps, each of which requires precision and attention to detail. The main processes include:
- Design and Engineering: The mold design process begins with the creation of a detailed 3D model of the mold using computer-aided design (CAD) software. The design must take into account all the factors mentioned earlier, including part design, material selection, cooling, ejection, and venting. Once the design is finalized, it is translated into a set of manufacturing instructions using computer-aided manufacturing (CAM) software.
- Machining: The mold components are typically manufactured using CNC (computer numerical control) machining, which allows for high precision and repeatability. The machining process involves cutting, milling, and drilling the mold components from a solid block of metal. The choice of machining method depends on the complexity of the mold and the required tolerances.
- Heat Treatment: After machining, the mold components may undergo heat treatment to improve their hardness and durability. Heat treatment processes such as annealing, quenching, and tempering are commonly used to enhance the mechanical properties of the mold material.
- Surface Finishing: The surface finish of the mold is critical for achieving the desired surface quality of the final plastic part. Surface finishing processes such as polishing, grinding, and coating are used to achieve the required finish. The choice of surface finish depends on the type of plastic being molded and the desired appearance of the final product.
- Assembly and Testing: Once all the mold components have been manufactured and finished, they are assembled into a complete mold. The mold is then tested to ensure that it functions correctly and produces parts that meet the required specifications. Any issues identified during testing are addressed before the mold is put into production.
Applications of Plastic Molds
Plastic molds are used in a wide range of industries to produce a variety of products. Some of the most common applications include:
- Automotive Industry: Plastic molds are used to produce a wide range of automotive components, including interior trim, dashboards, bumpers, and engine covers. The use of plastic molds in the automotive industry allows for the production of lightweight, durable, and cost-effective parts.
- Consumer Goods: Plastic molds are widely used in the production of consumer goods such as toys, kitchenware, and electronic housings. The ability to produce complex shapes and intricate details makes plastic molding an ideal choice for these applications.
- Packaging: The packaging industry relies heavily on plastic molds for the production of containers, bottles, and other packaging materials. Blow molding and thermoforming are commonly used processes in this industry.
- Medical Devices: Plastic molds are used to produce a variety of medical devices and components, including syringes, IV tubes, and surgical instruments. The use of plastic molds in the medical industry allows for the production of sterile, disposable, and cost-effective products.
- Electronics: Plastic molds are used to produce housings, connectors, and other components for electronic devices. The ability to produce parts with precise dimensions and complex geometries makes plastic molding an ideal choice for the electronics industry.
Conclusion
Plastic molds are indispensable tools in the manufacturing industry, enabling the mass production of a wide range of plastic products. The design and manufacturing of plastic molds require careful consideration of various factors, including part design, material selection, cooling, ejection, and venting. With advancements in technology, the precision and efficiency of plastic molds continue to improve, allowing for the production of increasingly complex and high-quality plastic parts. As the demand for plastic products continues to grow, the importance of plastic molds in the manufacturing process will only continue to increase.